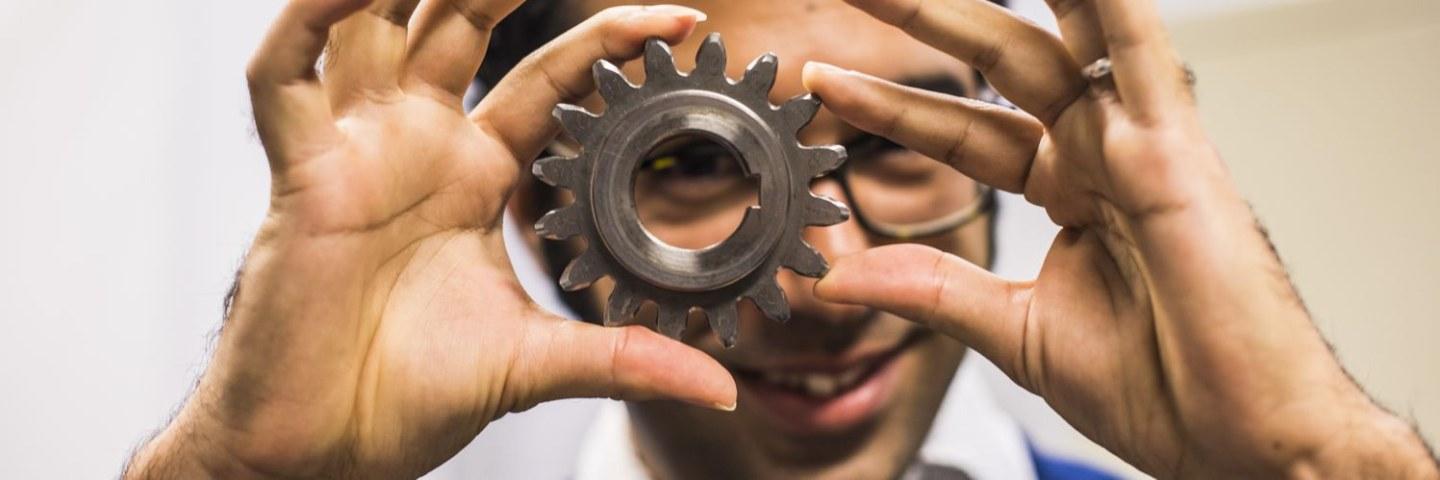
Tribology and wear testing
Tribology and wear testing infrastructure
Tampere Wear Center (TWC) is a research infrastructure for tribology and wear testing. It concentrates on both scientific and practical aspects of wear and tribology, bridging the gap between scientific basic research and applied industrial research and product development. The aim of TWC is to provide in-depth insight into the mechanisms of wear and thereby facilitate the development of new wear resistant materials and to find solutions to the practical wear problems constantly faced by the industry. .
The TWC infrastructure has facilities for wear and tribology testing, including heavy abrasion, impact wear, slurry-erosion, fretting and tribology of machine elements, such as gears, bearings, and frictional joints. The equipment is designed and built to simulate the in-service conditions. The facilities cover also ultrasonic surface modification, vibration monitoring, and diagnostics of machine systems.
