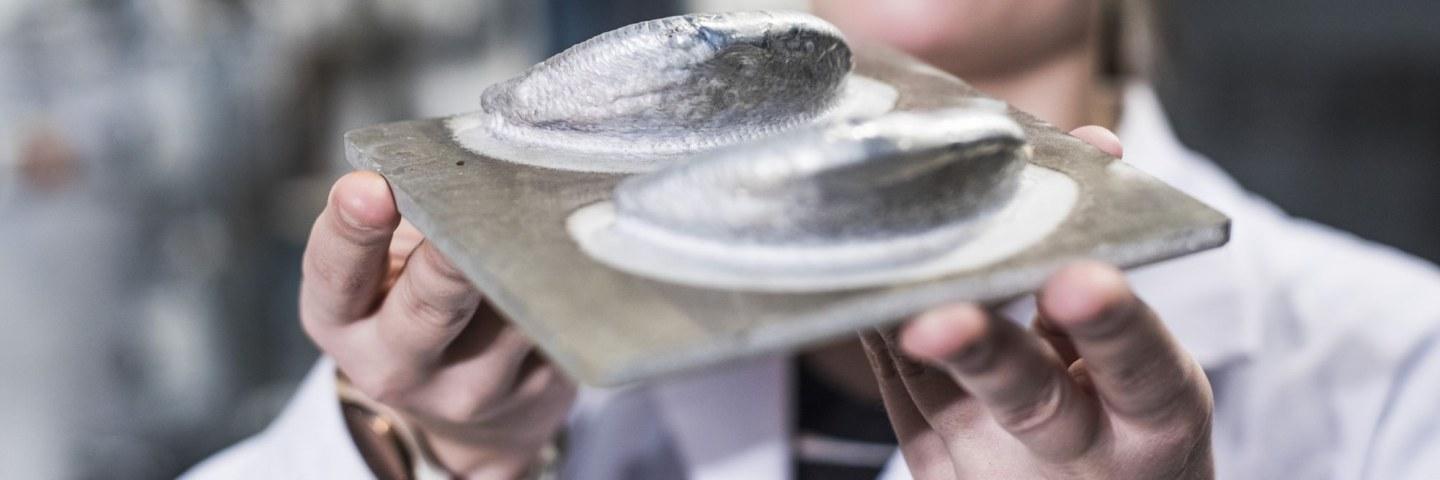
Research infrastructure
Coating techniques
Tampere University
Hervanta Campus
Tampere
Coating techniques
Facilities for the research and development of advanced thermal spray, weld, laser and thin film coatings. Novel coating processes with sophisticated process parameter optimization, including plasma, HVAF, cold spray, suspension spraying, weld, and laser technologies.
