High-speed and sustainable metal deposition process helps industry to protect machinery against corrosion and wear
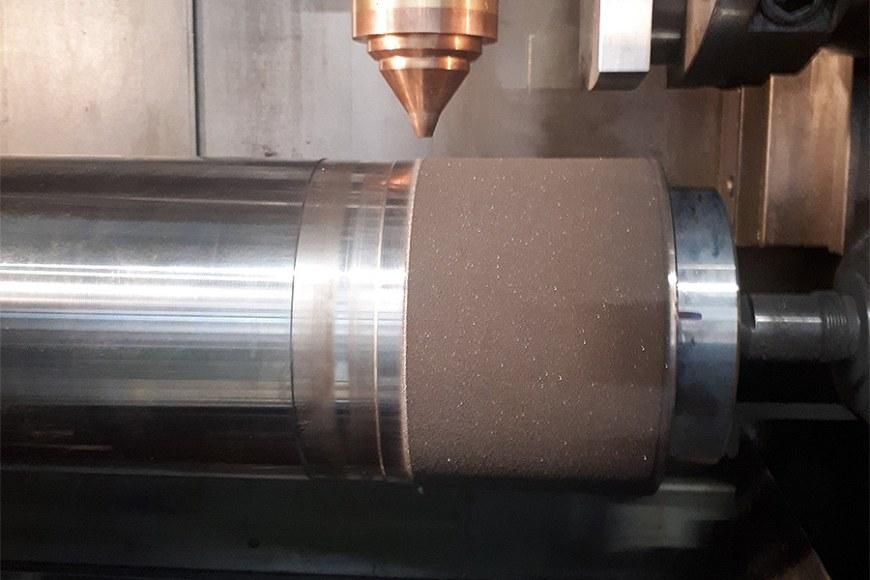
Extreme High-Speed Laser Cladding (EHLA) is a high material efficiency coating method combining the advantages of laser cladding and thermal spraying. EHLA can be used to produce thin, fully dense, fusion-bonded, high-quality metal and metal matrix composite coatings on top of a variety of alloys with high productivity. Coatings can be produced at a rate of approximately one square metre per hour.
“The method combines the high productivity of thermal spraying, high surface quality and low heat input with the excellent adhesion and corrosion resistance of the laser cladding,” says Senior Research Fellow Jari Tuominen, who leads the NOPSA - High-speed metal deposition for the benefits of industry at Tampere University.
The method was originally developed by the Fraunhofer Institute in Germany and is based on traditional laser powder cladding. Advantages of laser powder cladding are a wide range of additives, possibility to mix powders and add hard particles, solid lubricants and nucleating agents to achieve desired properties.
The main difference between EHLA and conventional laser powder cladding is higher power density (W/mm2) achieved by using a smaller focal spot (Ø1–2 mm). With high power density, a high traverse speed (~20–100 m/min) allows producing thin (0.1–0.5 mm) single layer depositions with low dilution. Small particle size (10–50 µm) of the powder used as primary material enables precise targeting of the powder jet even at a smaller focal point.
“Worldwide, the method is a substitute for environmentally hazardous and carcinogenic hard-chromium plating. It is a more environmentally sustainable choice because it is material efficient and does not cause direct emissions to the environment,” Tuominen says.
High-speed laser cladding offers several times the hardness of wear-resistant steels
In the NOPSA project, researchers are exploring the potential of the EHLA method in different types of corrosion protection and hard coatings’ production, as well as in repairing or remanufacturing damaged machine parts. The project, which started in January 2022, has so far produced, for example, nickel-based corrosion protection coatings on top of steels (S355, 42CrMo4) and cast irons.
The method’s suitability for 3D printing of metals by direct deposition will also be investigated, in addition to the study and production of coatings.
"The knowledge gained will be transferred to the manufacturing (mining & drilling, power plants, power transmission & gears) and maintenance (engines, pulp & paper),” says Tuominen.
The EHLA equipment at Tampere University consists of a CNC-controlled lathe, a continuous wave fibre laser (3kW) operating at a wavelength of about one micrometre, a powder feeder with two powder feed hoppers and a coaxial powder feeding head. For the cladding of flat parts, a kinematic parallel robot is used to move the part to be deposited. With the two powder feed hoppers and on-the-fly adjustment of powder proportions it is possible, for example, to produce different multi-material and gradient structures.

The image shows cross-sections of machined Inconel 625 coatings on top of ductile and grey cast iron. The coatings have a thickness of about 170–180 µm and an iron content of about 2–3 percentage of weight. The depth of the heat affected zone (HAZ) is a few tens of micrometres. The coatings’ corrosion resistance has been verified in a 750-hour salt spray test.

In hard coating production, chromium carbide and tungsten carbide nickel matrix coatings have been prepared on top of S355 and 42CrMo4 steels (Image 3).

The coatings have a microhardness of more than 1000 Vickers, which is 2–3 times higher than that of wear resistant steels. By adjusting the carbide content, coatings’ wear resistance has been matched to hard chromium’s wear resistance (~950 HV0.3) in a rubber wheel abrasion test.

The NOPSA project is funded by the European Regional Development Fund REACT-EU as part of the European Union’s response to the COVID-19 pandemic.
Further information
Jari Tuominen
+358 40 849 0196
jari.tuominen [at] tuni.fi