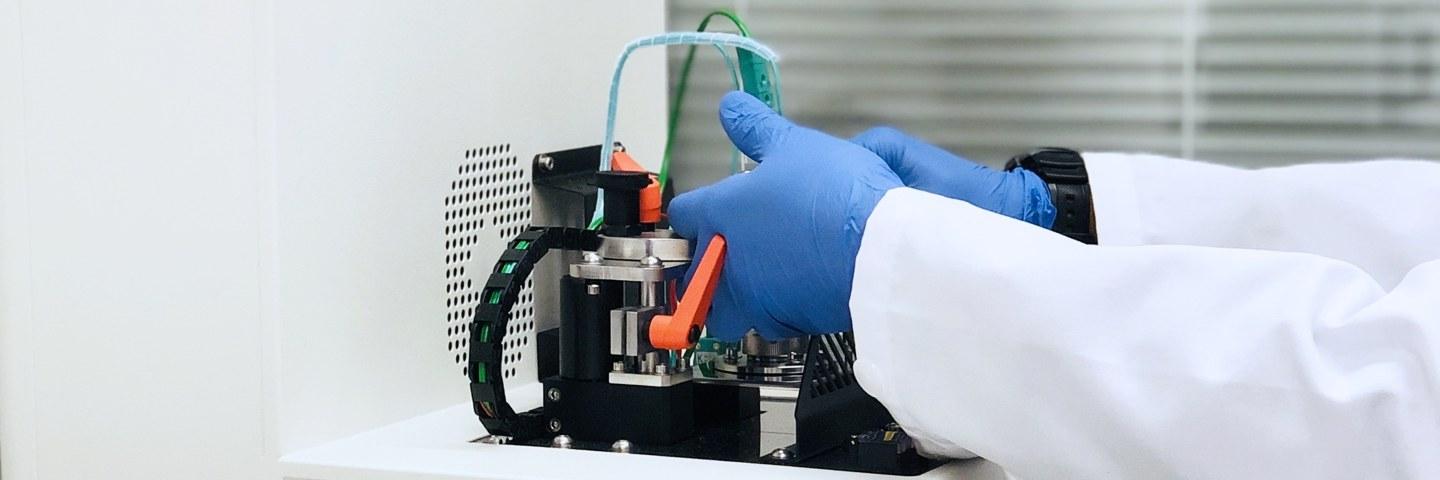
Research infrastructure
Energy and biorefining
Tampere University
Hervanta Campus
AddressKorkeakoulunkatu 8, Festia
Tampere
Facilities of Energy and Biorefining investigates thermal conversion of fuels and feedstocks. These are for example pyrolysis, gasification and combustion, liquefaction, catalytic pyrolysis, chemical looping process, hydrothermal processing and aqueous phase reforming. With these conversion techniques, various biomass and waste materials can be converted into high-refining value energy products.
