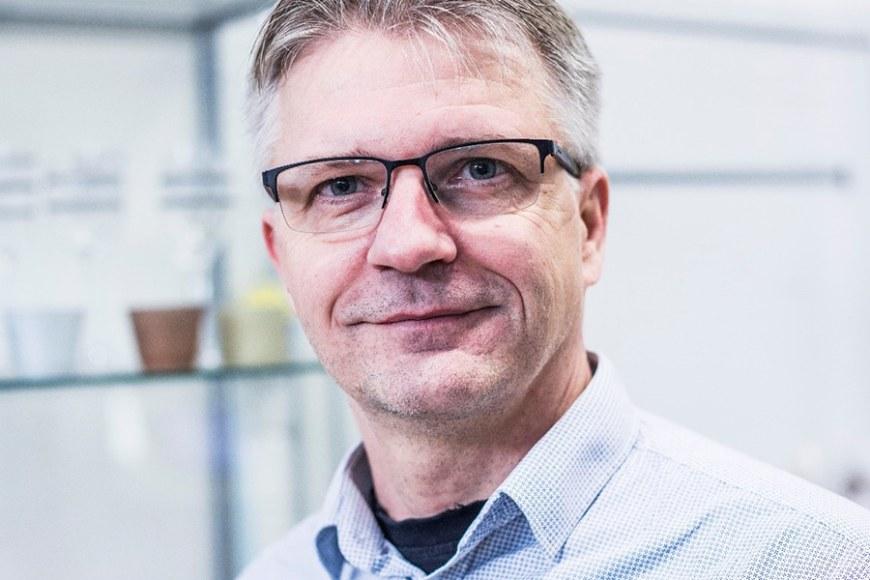
Thermally sprayed carbide coatings have been used successfully in many critical applications such as hydraulic cylinders, aircraft landing gear, paper machine rollers, ball and gate valves, pumps, and several other components that require wear resistance. The variation in properties and performance due to the coating process and manufacturing parameters of the same coating material can be wide.
The choice of coatings and coating processes is often complicated by the lack of information on how different manufacturing processes affect the performance of the coating. For example, hardness, porosity and adhesion are typically determined for thermally sprayed coatings, but there are many other factors, such as the magnitude of residual stresses inevitably generated in the coating during the manufacturing process, which may affect its performance.
“It is possible that customers of coatings may not be familiar with all the different manufacturing processes and their differences, but they must select and approve the supplier of the coating and determine the property requirements that the coating should meet. However, the requirements for coatings do not always directly indicate their performance in applications. It is often not even known which properties of the coating are critical to the performance of the coating, which is why scientific research is necessary,” Tommi Varis explains.
Thermal spraying has many interacting variables that are challenging to control. Often, insufficient attention has been paid to the management of factors resulting from the manufacturing process. Particularly, the effect of residual stresses on the coating properties is largely unknown. However, residual stresses have been shown to have a significant effect on, for example, the wear resistance and fatigue resistance of coatings. Therefore, more attention must be paid to their control. Varis, together with the cooperation network, wanted to develop concepts for measuring the residual stresses generated during coating manufacturing, to look at how different thermal spraying processes and the parameters affect residual stresses, and how they relate to coating properties, especially wear resistance. The study utilized the expertise knowledge of manufacturers of monitoring equipment companies Oseir Oy (Finland) and Reliacoat Technologies, LLC (USA). Additionally, measurement concepts were developed in collaboration with Stony Brook University (USA).
“There are several tools for monitoring the coating manufacturing process that provide information about the coating process in-situ. This is important in order to obtain consistent process data from coating processes to reliably compare coating properties, and to have a more understanding of the coating formation process on a scientific basis. The data typical of different coating methods can be utilized more generally for adjustment the stress states of the coatings for example with the help of analytical models,” Varis says.
Tommi Varis is originally from Kotka and currently works as a project manager at the University of Tampere, where he develops coatings mainly together with the Finnish coating industry.
The doctoral dissertation of M.Sc. Tommi Varis in the field of materials science Approaches for Linking the High Kinetic Thermal Spray Process, Residual Stresses and Coating Performance by Utilizing In-situ Monitoring will be publicly examined in the Faculty of Engineering and Natural Sciences of Tampere University on Friday 15.1.2021 starting at 12 in the lecture hall K1702 of the Konetalo building, Korkeakoulunkatu 6. Doctor Jiří Matějíček from Institute of Plasma Physics
Czech Republic and professor Hanlin Liao from University of Technology of Belfort-Montbeliard
France will act as opponents. Professor Petri Vuoristo from Tampere University Faculty of Engineering and Natural Sciences will act as the custos.
The event can be followed via remote connection.
The dissertation is available online at http://urn.fi/URN:ISBN:978-952-03-1826-0.
Photo: Tampere University/Jonne Renvall