FieldLab helps companies into Industry 4.0 era
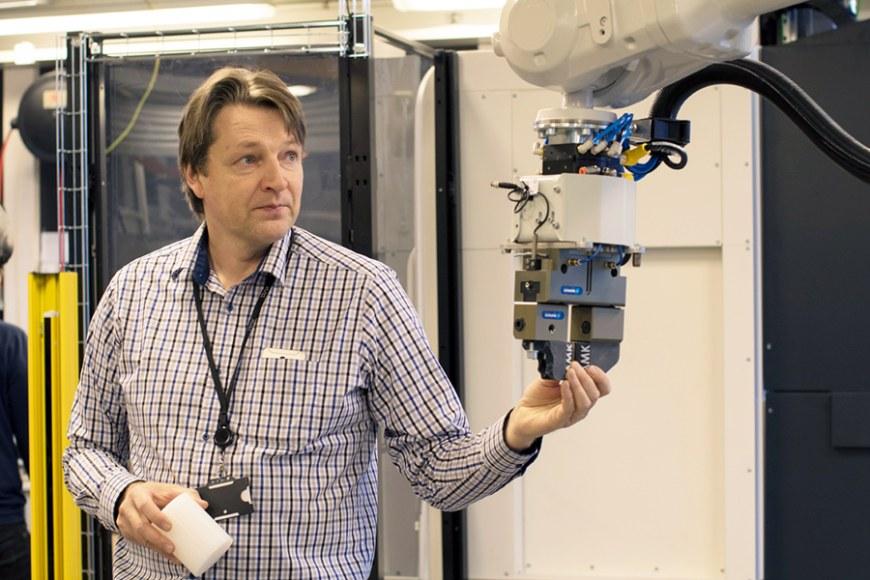
”However, FieldLab is more than just individual machines, cobots or robots; it is a platform to test an entire production process in Industry 4.0 operations”, Principal Lecturer Mika Ijas from Tampere University of Applied Sciences explains.
Industry 4.0, that sometimes is even called the fourth industrial revolution, means connecting the entire production chain to smart digital technology and networks. Automation, machine learning, interconnectivity and real-time data from each step of the operations lead way to both new business opportunities and to improved productivity.
FieldLab addresses industry needs
In manufacturing industry subcontracting chains can nowadays be very long and often even geographically dispersed. Industry 4.0 makes all production-related information available to everyone involved in the production – no matter where they are located. Through interconnected machines and IIoT (industrial internet of things) data from one machining unit is available in real-time for production scheduling and capacity planning for another unit at a different location.
”Industry 4.0 means connecting the entire production chain digitally. It goes far beyond just technology, new robots, or the amount of data they generate. It’s about making the operations intelligent from start to finish and about the benefits that companies gain from it. The benefits can materialize in many ways; be it improved product quality, reduced costs due to optimized resource consumption or improved energy-efficiency. But in the end, it must always mean money to the companies”, Ijas emphasizes.
Smaller companies that wish to take advantage of these benefits and work as subcontractors to large corporations already involved in Industry 4.0 will need to develop both new capabilities and their own production processes. FieldLab project was built on TAMK’s close collaboration with local businesses and previous projects, for example in 3D printing, which helped to recognize the challenges that smaller companies are facing when manufacturing is becoming smarter and ever moer digitalized. In particular subcontractors and mechanical engineering companies need to develop their competences in Industry 4.0. Ijas is pleased that TAMK can now address these needs.
”We can now offer the local companies a hands-on testing environment to demonstrate industry 4.0 operations and where the companies can even test their own processes”.
Collaboration and simulation with a digital twin
FieldLab will have its official opening in December on the main campus of TAMK. After that, it is time to welcome companies with their pilots to FieldLab. Apart from success stories Mika Ijas also awaits “failures” in the tests. By testing Industry 4.0 operations in FieldLab the companies can save hundreds of thousands in unnecessary investments if the benefits don’t fulfill the expectations. Even then the companies have gained new capabilities, knowledge, and experiences of Industry 4.0 thanks to FieldLab. This applies naturally also to the students of TAMK.
”FieldLab is also a great new learning environment for our students. The fact that the companies are present there makes it even an excellent platform for collaboration between students and businesses, which again is something that everyone benefits from”, Ijas says.
Towards the end of the two-year project also a digital twin, i.e. a digital replica, should be produced. A digital twin can be, for example, used to simulate the entire production process of a new product to calculate what is needed in production time, materials, etc. A subcontractor can then give an exact and realistic price for a new product, even before a single unit is produced physically.
FieldLab is part of an international network
TAMK’s FieldLab opens new opportunities for networking and knowledge sharing internationally. Being part of the international network of FieldLabs allows TAMK and its partners to gain from the expertise of FieldLabs in other countries. As an example, Ijas names a Dutch FieldLab specialized in the food industry.
”At TAMK we have gained a lot of experience in 3D printing. The new equipment in FieldLab, that can produce objects up to six meters wide and two meters high, brings our know-how to the next level. This is something that we can, in turn, offer to the international network”, Ijas explains.
FieldLab is a two-year project funded by the Finnish Ministry of Culture and Education. The project is part of development activities in one of TAMK’s research and development focus areas, Intelligent Machines and Smart Devices.
More information:
Mika Ijas, Principal lecturer, Intelligent Machines
Degree Programme in Mechanical Engineering | School of Industrial Engineering
+358 50 4471 189,
mika.ijas [at] tuni.fi (mika[dot]ijas[at]tuni[dot]fi)
Text: Helena Pekkarinen
Photo: Jaakko Saarilampi